What is the difference between a gate valve and a globe valve?
Pneumatic Valves: What Are The Different Types?
Here are the main types of pneumatic valves:
Directional Control Valves: These valves control the direction of airflow in a pneumatic system. Common types include 2-way, 3-way, and 4-way valves.
Pressure Control Valves: These regulate and maintain the pressure in a pneumatic system. Examples include pressure regulators, relief valves, and back pressure valves.
Flow Control Valves: These valves regulate the rate of airflow in the system. They include throttle valves, needle valves, and flow control valves.
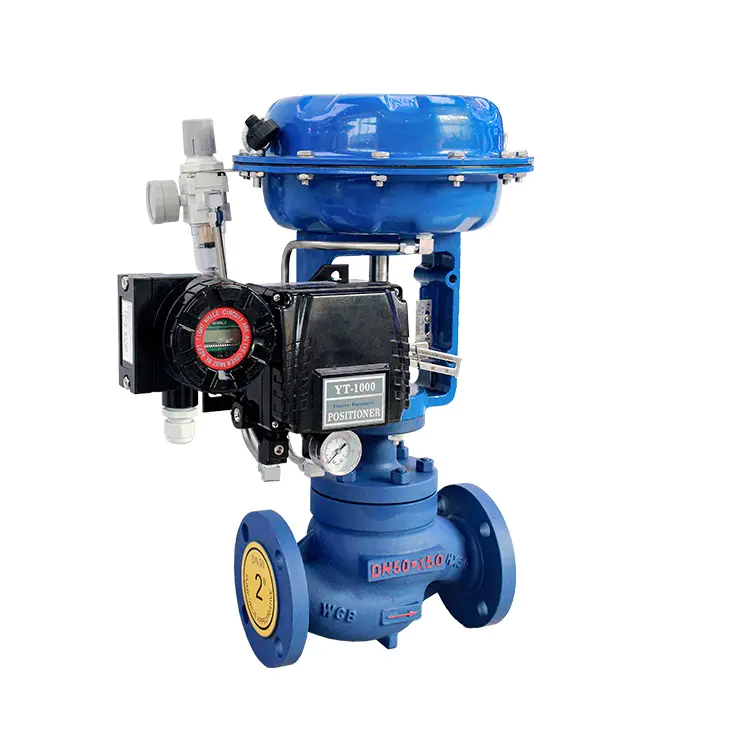
The specific type of pneumatic valve needed depends on the requirements of the particular pneumatic system and application. Factors like flow rate, pressure, and function all influence the valve selection.
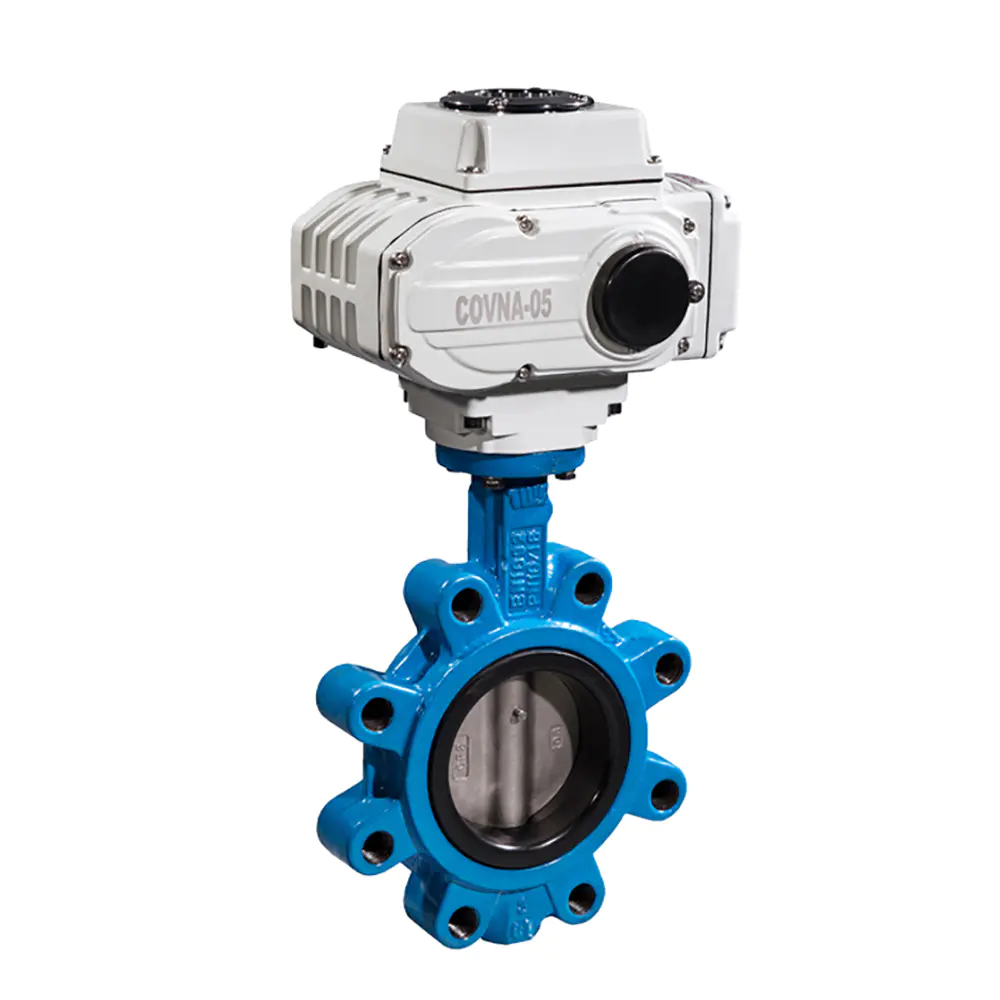
Electric control valves are essential components in various industrial processes, Here are the main types:
- Globe Control Valves
- Design: Characterized by a linear motion to control the flow. The valve body has a spherical shape, and the disk moves perpendicularly to the flow.
- Applications: Used for precise throttling and flow regulation in applications requiring accuracy and reliability.
- Ball Control Valves
Design: Utilize a ball with a hole through it, which rotates to allow or block flow. The flow is controlled by the position of the ball.
Applications: Suitable for applications requiring quick shutoff and tight sealing, such as in chemical processing and water treatment. - Butterfly Control Valves
Design: Use a disk that rotates around a central axis. The flow is controlled by the angle of the disk.
Applications: Ideal for large volume flows with lower pressure drops, commonly used in HVAC systems, water distribution, and slurry services. - Diaphragm Control Valves
Design: Employ a flexible diaphragm that moves up and down to regulate flow. The diaphragm separates the flow media from the actuating mechanism.
Applications: Used in applications requiring contamination-free operation, such as pharmaceutical and food industries. - Solenoid Control Valves
Design: Operated by an electromagnetic solenoid, which moves a plunger to open or close the valve.
Applications: Used for rapid on-off control in automated systems, common in irrigation, HVAC, and fluid power applications. normally open check valve. Alao is small electric valve. - Three-Way and Four-Way Control Valves
Design: Have three or four ports, respectively, to mix or divert flow. These valves can change the direction of flow between different paths. there have 1/2 gas shut off valve.3 way electric ball valve.
Applications: Utilized in heating and cooling systems, mixing processes, and complex piping systems.
Key Factors in Selecting an Electric Control Valve:
Flow Characteristics: Understanding the required flow rates and control precision.
Pressure and Temperature: Compatibility with the operating pressure and temperature ranges.
Fluid Properties: Considering the type of fluid (e.g., corrosive, viscous, abrasive) being controlled.
Actuation Speed: Requirements for the speed of valve actuation.
Installation Space: The available space for installing the valve in the system.
Maintenance Needs: Ease of maintenance and reliability over time.
Electric control valves are essential in various industries for their ability to provide precise and automated control of fluid systems. The choice of valve type depends on the specific requirements of the application and the properties of the fluid being controlled.
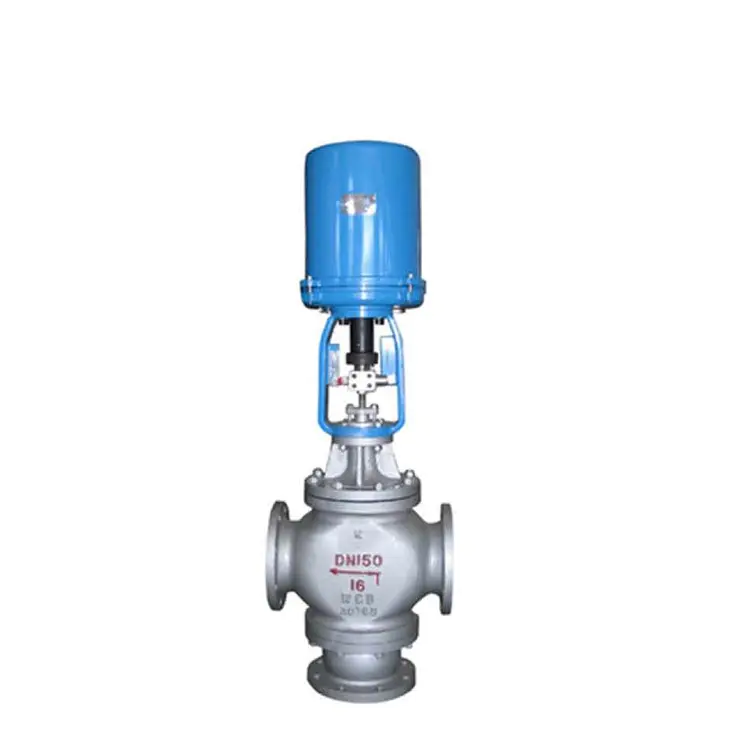
What is a Pneumatic Valve?
The primary function of a pneumatic valve, also known as a directional control valve, is to switch airflow. These valves can keep the pressure constant. There are numerous pneumatic valve categories and a wide range of pneumatic valves. Pneumatic valves are classified based on their style, type, design principle, operation type, function, size, and application.
The pneumatic valve can perform everything from switching a single flow path on and off to precise proportional control of pressure and flow. Most pneumatic valves have a control function, which can be defined as the operation of the valve in any process or the controlling of a quantity. A control function necessitates control energy, which can be determined by the mode of actuation, which can be manual, mechanical, hydraulic, or pneumatic.
What is the Operation of a Pneumatic Control Valve?
Pneumatic control valves can reduce pressure in a controlled manner by using actuators and positioners that are controlled by a controller. Controllers can detect pressure fluctuations and adjust the air supply signal to the pneumatic positioner. A pneumatic positioner would supply air to the diaphragm, allowing a valve to be opened. Springs are used as an opposing force, causing the valves to close when the air pressure applied to the diaphragm is lost or reduced. Many industries rely on pneumatic control valves.
Pneumatic Valve Types
Pneumatic valves, also known as directional control valves, can be configured in a variety of ways, including:
- By the number of flow ways or switching positions that are possible
- By the number of inlet and output ports they have
- By the mechanism used to open or close the ports
- By the status of the valve when it is not actuate
PDF Get-a-Product Catalogue