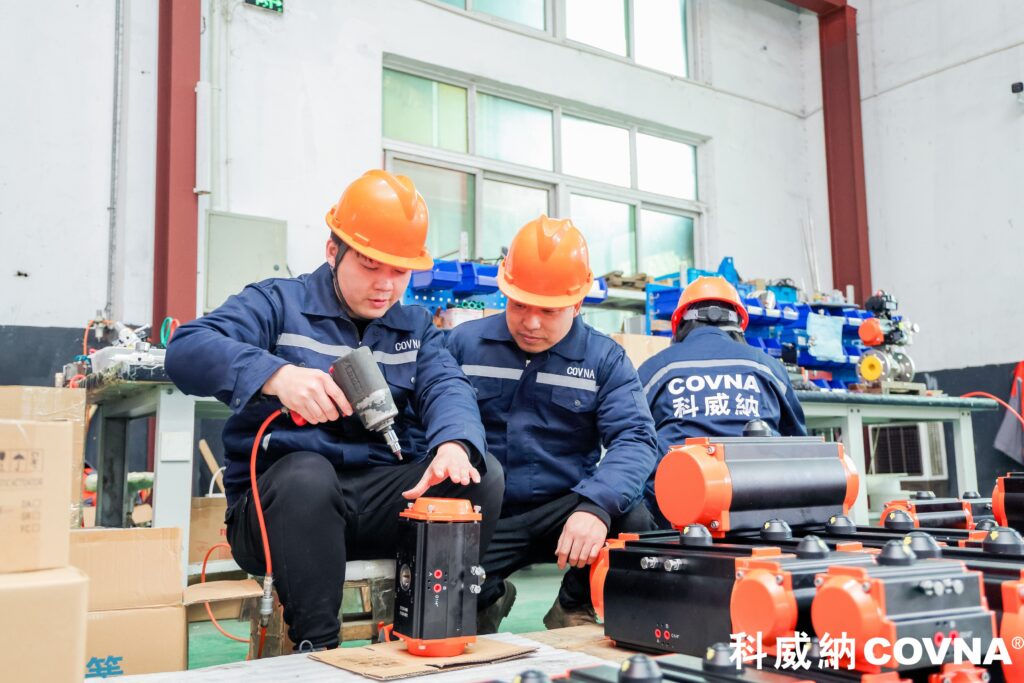
Steps for choosing the right actuator for your application
Choosing the right actuator for your application might not be as simple as it seems. Mentioned below are some steps will act as a guide for choosing the right actuator for your application.
1. Understanding the kind of movement that is required in the application
You must have a clear idea about the kind of movement that is required in your application project. Does the object or machine require rotary or linear movement? Linear actuators are beneficial in exerting a mechanical force move an object in a linear/straight line. On the other hand, rotary actuators help generate circular motion. Hence the kind of actuator you need to depend on the kind of mechanical movement your application requires.
2. Assess the level of precision that you need from the actuator
Precision levels vary from one actuator to another. While some actuators are best for heavy-duty work and work well in rugged and rough environments, some actuators are good for handling smaller, more detailed work. One of the best examples of handling small, detailed work is the packaging of certain products. This job needs precision and accuracy. Moreover, it is a repetitive action, which needs to be done continuously hundreds or even thousands of times in a single day.
Also Read: A Basic Guide to Human-Machine Interface
3. Take into consideration the energy input
There are various factors contributing to the popularity of electrical actuators. Machines with electrical actuators have become more flexible and are sophisticated enough for hand myriad operations. However, electrical actuators are not suitable for all kinds of work. If your work doesn’t include electrical voltage input, you should consider using pneumatic or hydraulic actuators instead.
4. Access the amount of force you require
The main purpose that an actuator serves is either lifting or moving an object. You must first find out the weight of the object that you need to move or lift. Every actuator has a load capacity, indicating the maximum amount of weight it can lift or move. Load capacities vary from one actuator to the other, though the actuators might have a resemblance in appearance. While buying an actuator, check that the object’s weight is in sync with the actuator’s load lifting or moving capacity.
5. Ascertaining the speed of the actuator
Depending on the project you are working on, the speed of the actuator is an important consideration that you have to keep in mind. Generally, projects, where actuators have to exert high force will move slowly when compared to the ones which generate low force. The measurement of the speed of an actuator is done in distance covered per second.
6. Find out the distance till which the object has to be moved
Stroke length is the technical term for the distance to which the object can be moved by an actuator. When choosing the right actuator, this distance is an extremely crucial factor. Actuators are available in different stroke lengths and this length should also act as one of the decisive factors when you are purchasing an actuator for your project or application.
7. Understanding the operating environment
While choosing an actuator for your application, do not forget to check the operating environment of the device. Find out if the actuator will be able to function in a dusty environment, if humidity poses a problem in operating the actuator, or if the actuator can work in an environment that is rugged and rough. It’s advisable that you look for an actuator which has a high protection rating as it would be suitable for all kinds of conditions.
Also Read: All About Ultrasonic Sensors & How They Work
8. Understand and then decide on the mounting style
There are different mounting styles of actuators which are available in the market. Before you decide to purchase an actuator for your project or application, make sure that you understand the kind of mounting of the actuator. One of the best examples is that of a linear electric actuator with a dual-pivot mounting method. With this mounting method, the device can pivot on both sides while retracting and extending. An application or project with this actuator will move on a fixed path and will also have two free pivot points.
Do you have any problems with selecting the actuator valves?
Don’t worry! Rose and Mandy will help you how to select the valve basic on your project’s need.
They will introduce the technical parameters and features of the valve for you. Please enjoy the video.
There is always one valve suitable for your project.
Selecting a suitable actuator valve for your project, particularly with the COVNA brand, involves several key considerations. Here’s a step-by-step guide to help you through the selection process:
1. Understand Your Application Requirements
Media Type: Identify the type of media (liquid, gas, steam) the valve will control. Different media may require specific materials to prevent corrosion or ensure safety.
Pressure and Temperature: Determine the operating pressure and temperature ranges. This will influence the choice of valve type and materials.
Flow Rate: Calculate the required flow rate. This will help in sizing the valve appropriately.
Valve Function: Decide on the function of the valve (e.g., on/off, flow control, mixing, diverting).
2. Valve Type Selection
COVNA offers various types of valves, including:
Ball Valves: Suitable for on/off control with low-pressure drop.
Butterfly Valves: Good for large diameter pipes with lower pressure drops.
Globe Valves: Ideal for precise flow control.
Gate Valves: Typically used for on/off services with minimal pressure drop.
3. Actuator Type Selection
COVNA provides different actuator options:
Electric Actuators: Ideal for precise control and remote operation. Consider power supply (AC/DC) and any special requirements like explosion-proof or fail-safe features.
Pneumatic Actuators: Suitable for applications requiring quick response times and high torque. Ensure the availability of compressed air.
Hydraulic Actuators: Used for high force applications, less common but necessary in specific industries.
4. Material Compatibility
Ensure that the valve materials (body, seal, and internal components) are compatible with the media. Common materials include:
Stainless Steel: Resistant to corrosion, suitable for a wide range of applications.
Brass: Often used for water and non-corrosive media.
PVC/Plastic: Suitable for low-pressure and corrosive media.
5. Size and Specifications
Valve Size: Based on your flow rate and pipeline size.
Connection Type: Flanged, threaded, welded, etc., based on your system design.
End Connections: Ensure compatibility with your existing pipeline system.
6. Control Requirements
Manual vs. Automated: Determine if manual operation is sufficient or if automation is needed.
Control Signals: For automated systems, consider the type of control signals (4-20mA, 0-10V, etc.).
7. Industry Standards and Certifications
Ensure the valve meets relevant industry standards and certifications for your specific application (e.g., ISO, API, CE).
8. Maintenance and Support
Consider the ease of maintenance and the availability of technical support and spare parts from COVNA.
9. Cost and Budget
Balance the cost of the valve and actuator with your budget constraints while ensuring you meet all technical requirements.
10. Consult with COVNA Experts
Leverage COVNA’s expertise by consulting with their technical support team. They can provide detailed product information and help ensure you select the most suitable valve and actuator for your project.
Summary
Selecting the right actuator valve involves careful consideration of your project’s specific needs and technical requirements. By following these steps and consulting with COVNA’s experts, you can ensure a successful selection and implementation.
For more detailed information on COVNA products, you can visit Our official website or contact our customer support.
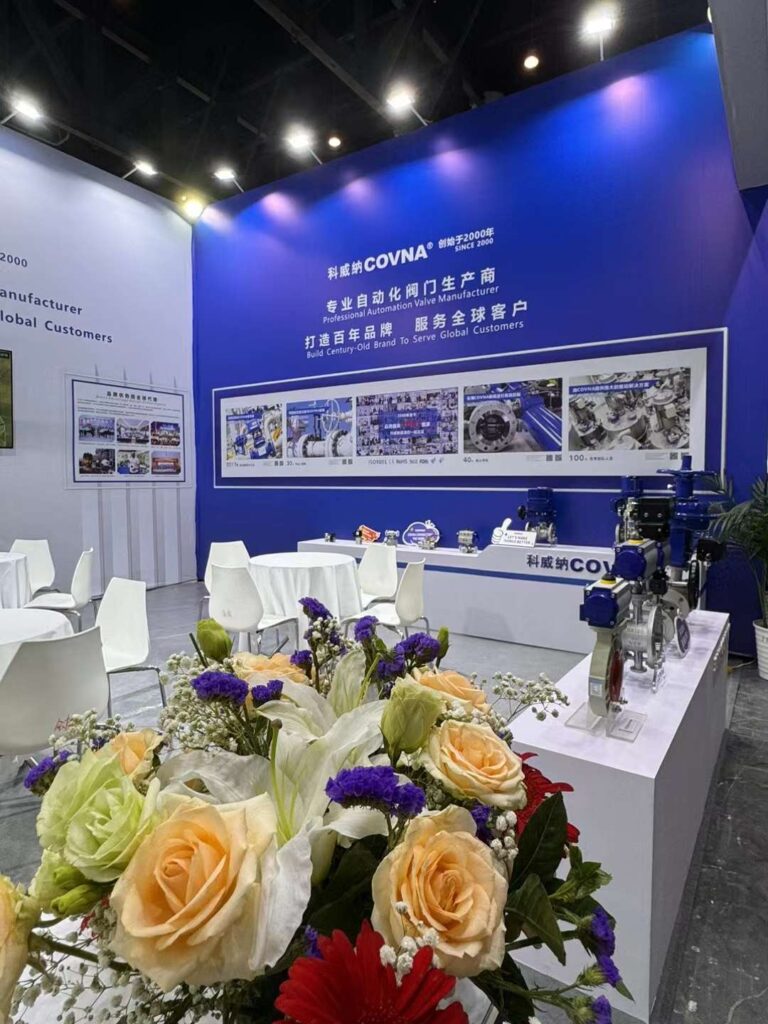
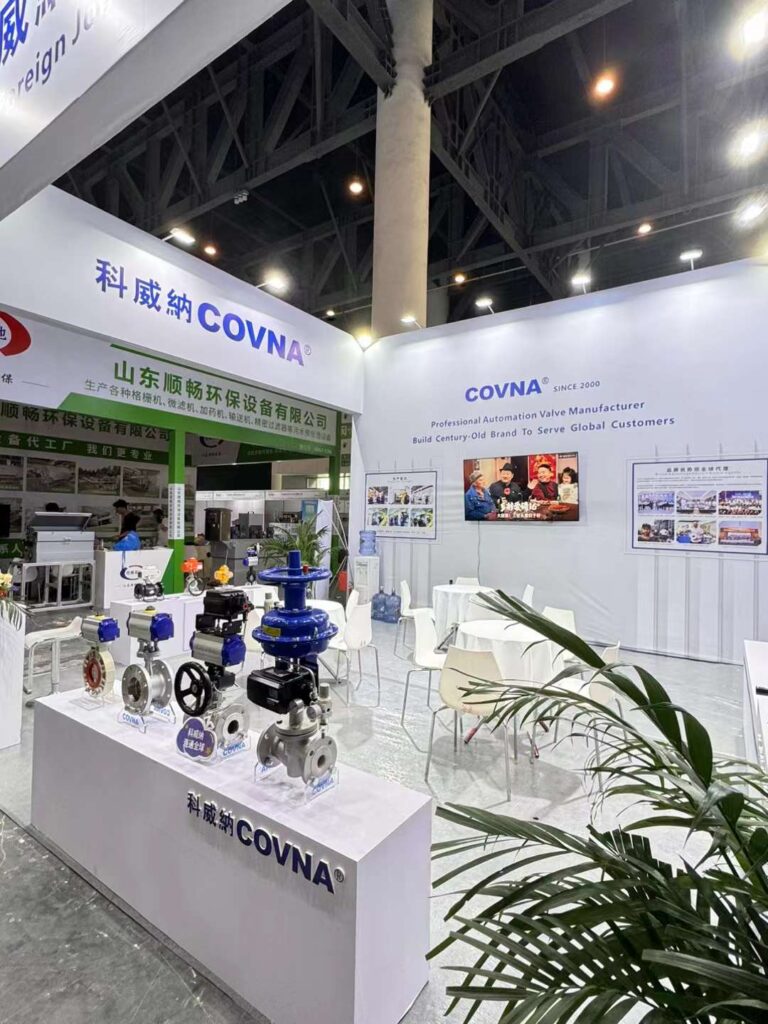
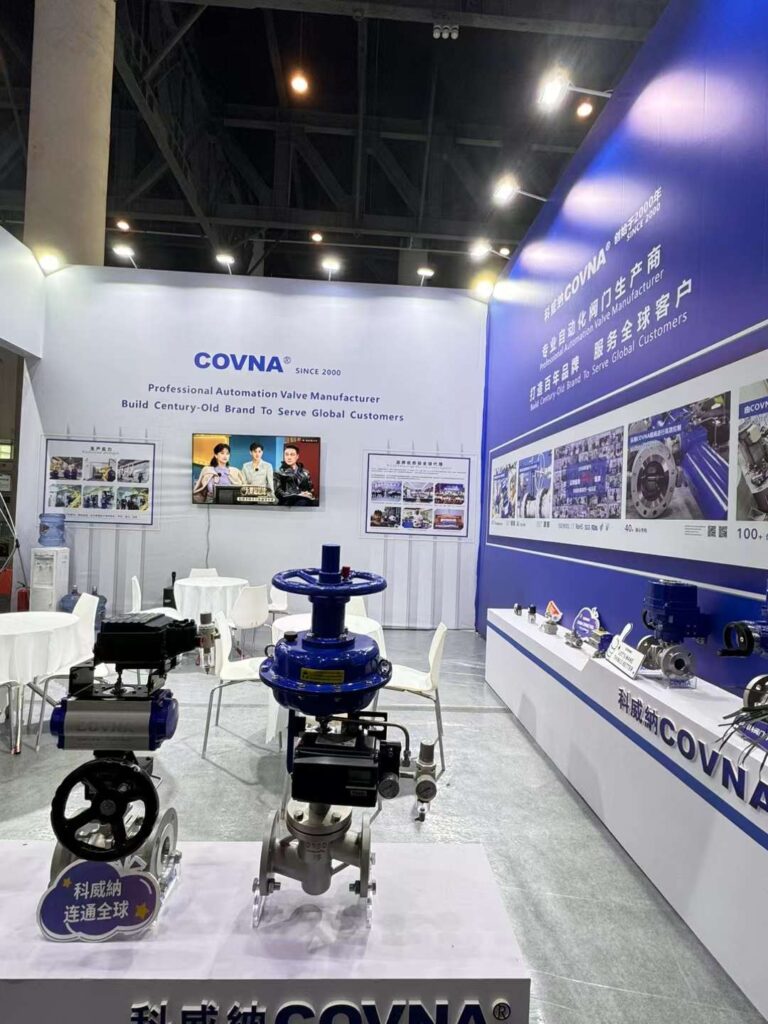
PDF Get-a-Product Catalogue