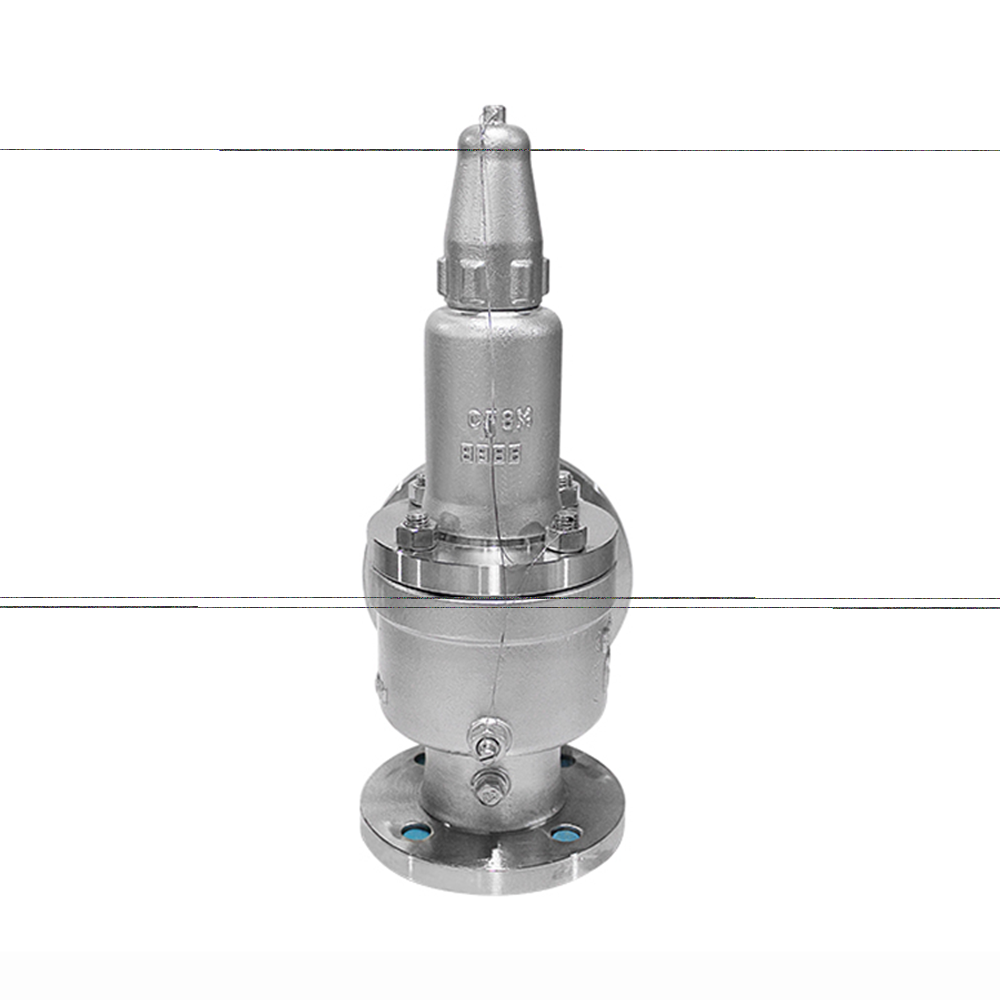
Safety valve: the core component of industrial equipment safety protection
In industrial production and pressure vessel systems, safety valves, as key overpressure protection devices, undertake the important mission of preventing equipment explosions, ensuring personnel safety and maintaining stable system operation. Whether it is petrochemical, electric power, or pharmaceutical and food processing industries, safety valves are an indispensable link in the equipment safety chain. This article will explore in depth the working principle, classification, application scenarios and selection points of safety valves to help users better understand this key equipment.
1. Working principle of safety valves
The core function of safety valves is to control system pressure by automatically releasing media (such as gas, liquid or steam). When the internal pressure of the equipment exceeds the preset set pressure, the valve flap opens under the action of pressure and quickly releases excess pressure; when the pressure returns to normal, the valve flap closes again to ensure the continuous operation of the system. This process relies on precise spring force or lever counterweight design, which reflects the “active protection” characteristics of safety valves.
2. Main classification of safety valves
According to the structure and working principle, safety valves can be divided into the following categories:
Spring-type safety valve: uses spring force to balance the medium pressure, has a compact structure, and is suitable for a variety of industrial scenarios.
Lever safety valve: The opening pressure is adjusted by lever and hammer, and it is often used in low-pressure and high-flow systems.
Pilot safety valve: The pilot valve is used to control the action of the main valve, with high precision, and is suitable for high-pressure and high-parameter working conditions.
In addition, it can be subdivided into steam safety valves, gas safety valves and liquid safety valves according to the type of media. Users need to choose the appropriate model according to actual needs.
Key application areas of safety valves
Petrochemical industry: Protect reactors, storage tanks and pipeline systems from overpressure risks.
Power industry: Used for overpressure protection of equipment such as boilers and steam turbines.
Pharmaceutical and food processing: Ensure the safe operation of clean pressure vessels.
New energy field: Pressure control in hydrogen energy storage and transportation, and lithium battery production.
In these scenarios, the reliability and response speed of the safety valve are directly related to production safety and economic benefits.
4. Key parameters for safety valve selection
When purchasing a safety valve, you need to pay attention to the following parameters:
1. Set pressure: The preset pressure value for valve opening must meet the equipment design standards.
2. Discharge capacity: The medium flow rate that can be released per unit time must match the maximum overpressure condition of the system.
3. Medium characteristics: Factors such as corrosiveness, temperature, phase state (gas/liquid) affect material selection (such as stainless steel, alloy steel).
4. Certification standards: Comply with international or industry standards such as ASME, API, GB/T to ensure compliance.
5. Maintenance and inspection of safety valves
Regular maintenance is the key to ensuring the long-term stable operation of safety valves:
Online inspection: Use acoustic detection technology or pressure sensors to monitor the valve status.
Offline calibration: Disassemble and inspect at least once a year to calibrate parameters such as spring force and sealing.
Fault warning: Pay attention to problems such as valve leakage, rust or start-up delay, and replace accessories in time.
As the “last line of defense” for industrial safety, the selection, installation and maintenance of safety valves must strictly follow technical specifications. With the development of intelligent technology, intelligent safety valves with remote monitoring and self-diagnosis functions are gradually becoming an industry trend. Whether it is traditional industrial upgrading or emerging field applications, the innovation of safety valves will continue to escort global industrial safety.