Wafer check valves are available in many sizes, typically from 2” to 24”, support customize bigger size. Body styles include wafer, lug, double flanged and extended body. Wafer check configurations are available in retainer-less style, wafer, extended body wafer and lined. Typical body materials are cast iron, ductile iron, WCB cast steel, 316 stainless steel and other alloys. Common seating materials are EPDM and Viton.
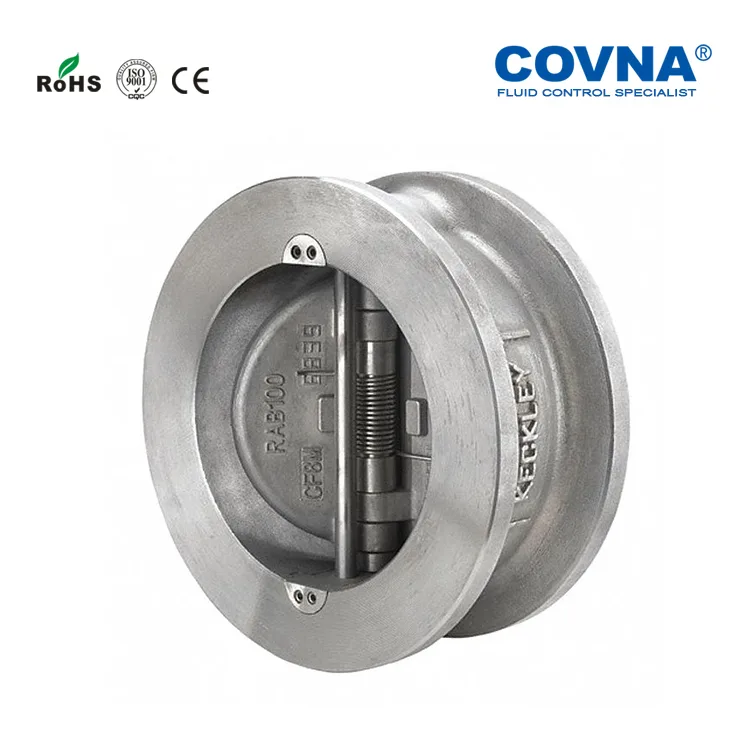
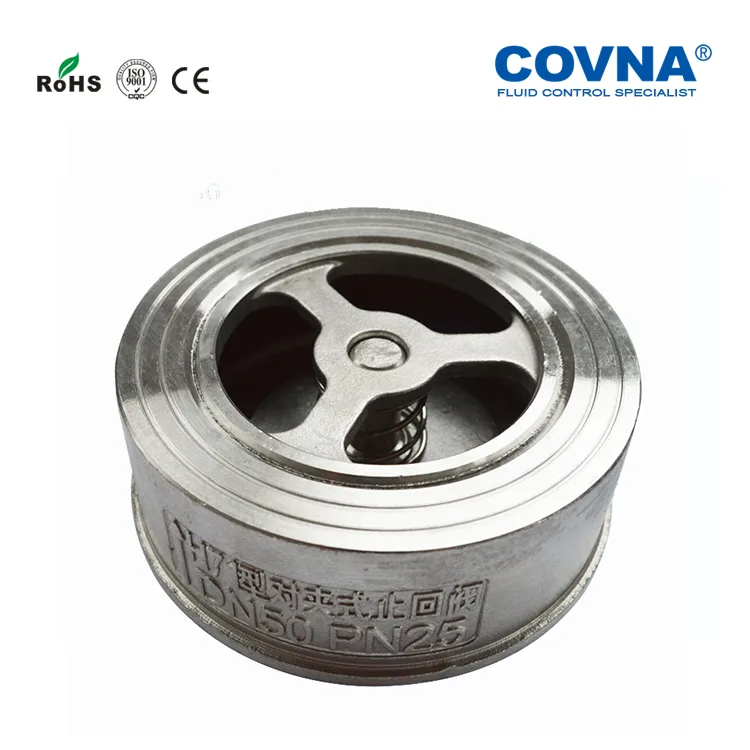
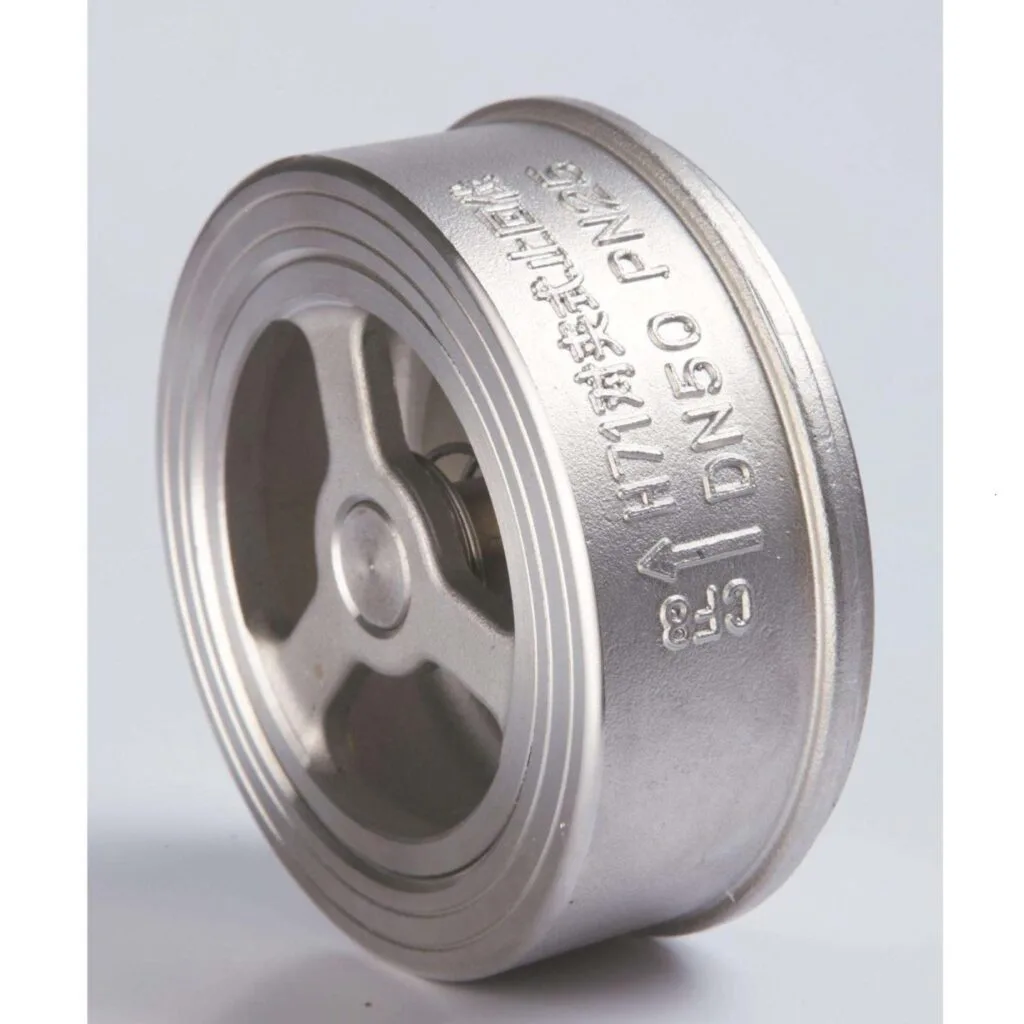
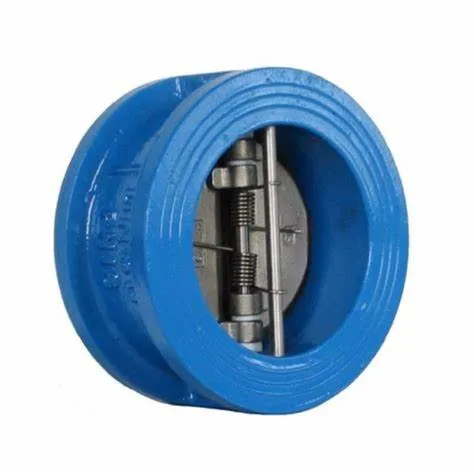
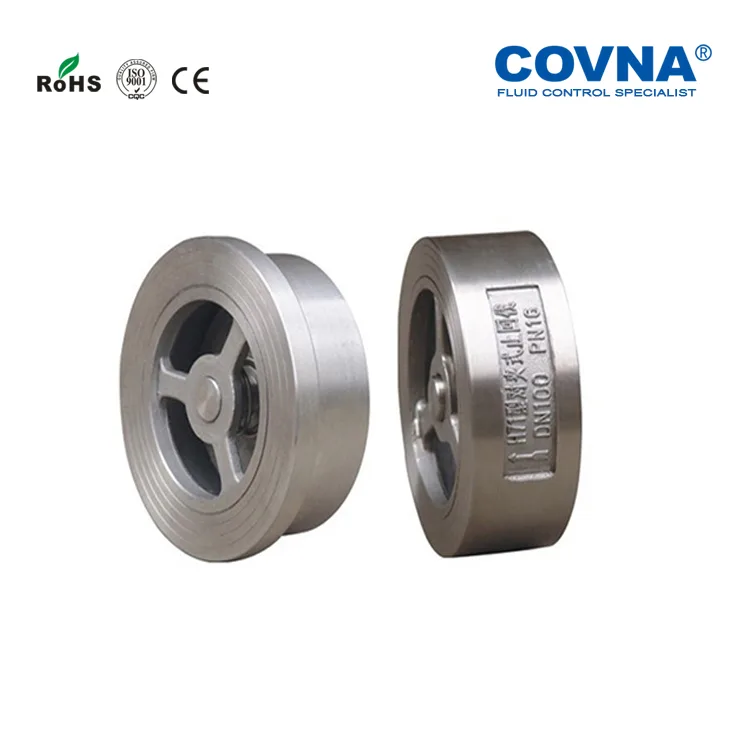
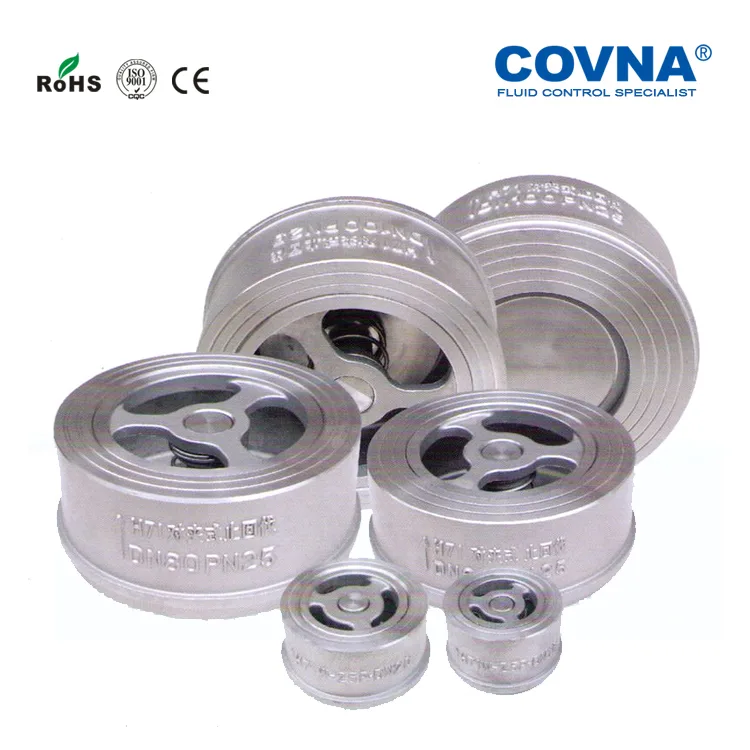
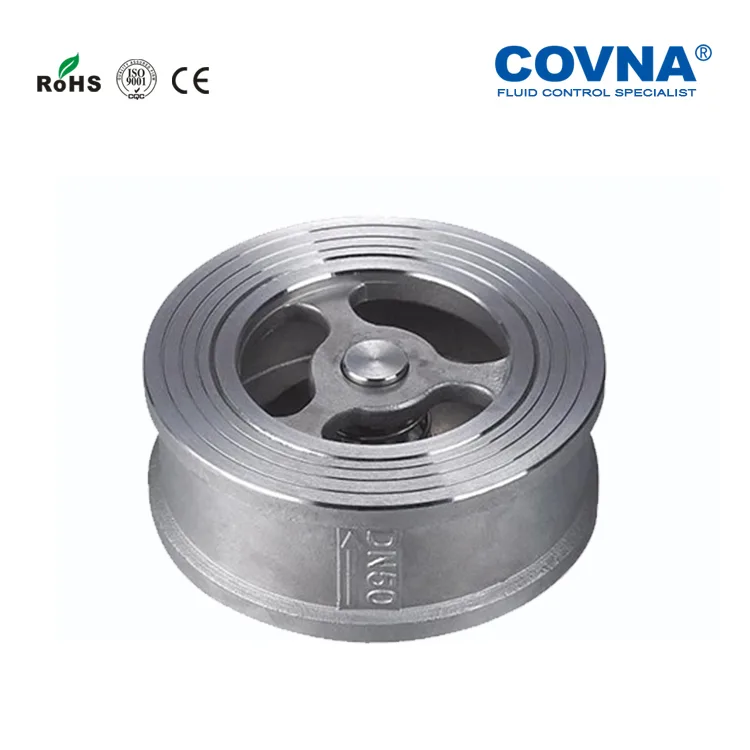
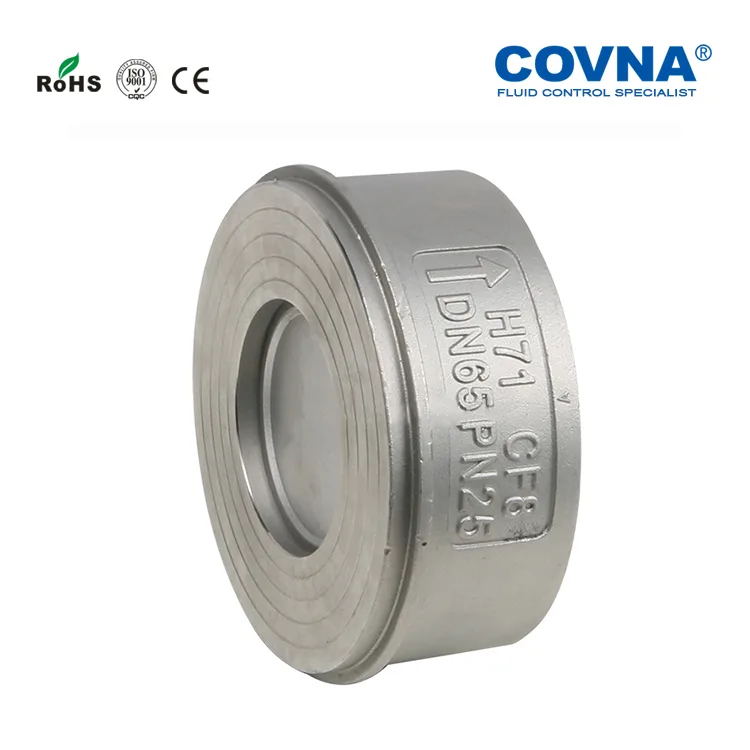
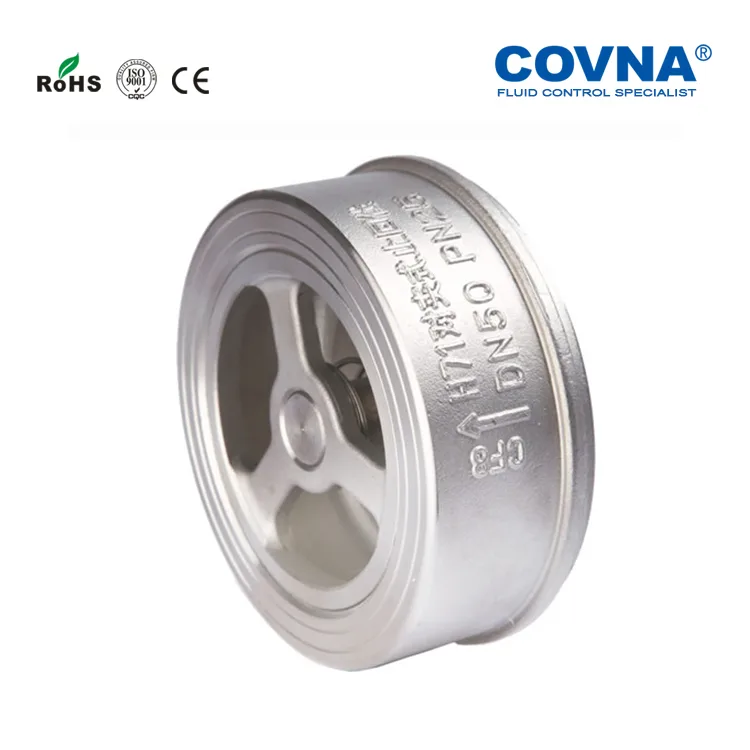
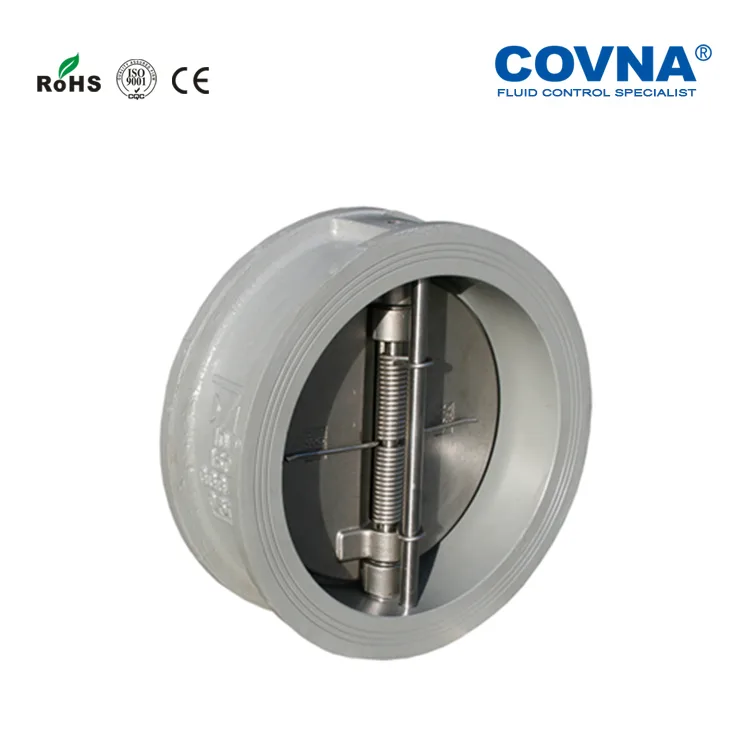
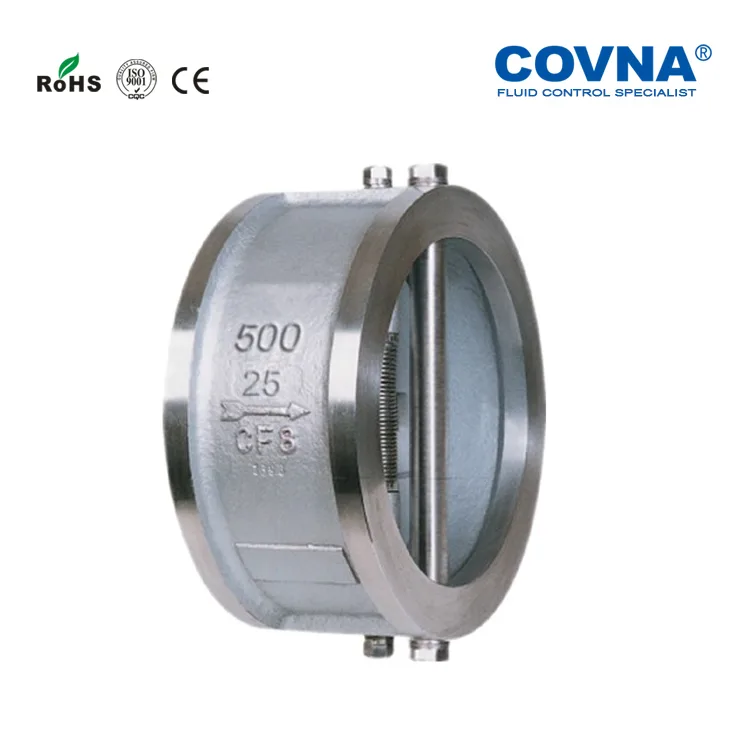
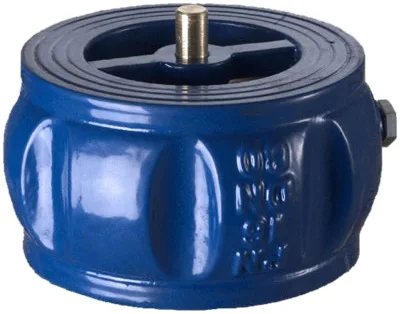
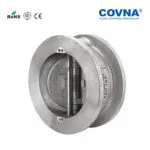
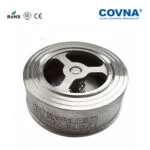
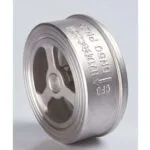
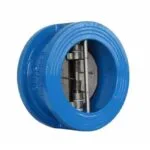
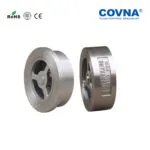
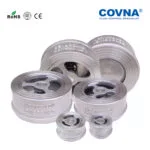
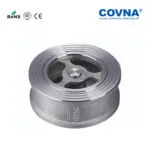
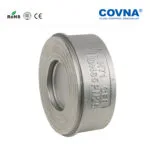
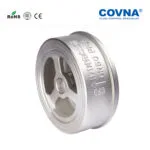
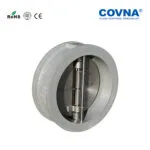
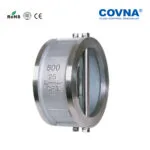
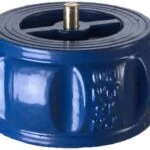
COVNA Dual Plate Wafer Type Spring Check Valve
- Model: Check Valve
- Size Range: 2″ to 24″
- Pressure Range: 16Bar
- Material: WCB, Stainless Steel
COVNA Dual Plate Wafer Type Check Valve
• Low Pressure Drop (High Cv)
• Light Weight ( Reduces weight by 80–90% compared to conventional Flanged check valves )
• Lower Cost (Light weight, compact profiles and the elimination of flanges allows )
• Alleviates Water Hammer ( Designed to close our valves quickly.
Which assures high performance and eliminating chatter )
• Easier to install, remove and replace in both new and existing piping
systems.
• Retainerless Design ( Ideal for critical applications where valve body penetration and the possibility of leakage cannot be tolerated )
COVNA Double Disc Check Valve Export Destination Worldwide
USA | United Kingdom | Kuwait | Bahrain | Qatar |
Saudi Arabia | Germany | Oman | Singapore | Malaysia |
France | Iran | South Africa | Turkey | Indonesia |
Brazil | India | Colombia | Iraq | Chile |
Argentina | UAE | Nigeria | Sudan | Jordan |
Ecuador | Netherlands | South korea | Vietnam | Thailand etc. |
Wafer check valve are used in both horizontal and vertical (upward) flow applications. For horizontal flow applications, the shaft should be vertically oriented to the pipeline. For vertical (upward) applications, the shaft should be perpendicular to the piping.
1.Oil and Gas Industry
Pipeline Flow and Pressure Control: Used for flow and pressure control in natural gas and oil pipelines to ensure stability during transportation.
Gas and Liquid Distribution Systems: Regulates the flow of gases or liquids, ensuring precise control under various operating conditions.
Automation of Distribution Systems: Used in refineries and natural gas processing plants to automate fluid distribution and regulate the reaction processes.
2.Chemical and Petrochemical Industry
Reactor Pressure and Flow Control: Used in chemical reactors, storage tanks, and other equipment to control pressure and flow, ensuring stability in the chemical reaction process.
Flow/Pressure Regulation: Regulates the flow of liquids or gases in processes such as polymerization, refining, and distillation to ensure efficient production.
Steam Control: Regulates the flow and pressure of steam in steam generators and distribution systems.
3.Water and Wastewater Treatment
Water Flow Control: Regulates water flow and pressure in water supply and wastewater treatment systems to ensure normal operation.
Gas and Chemical Additions: Regulates the flow of chemicals or gases (such as chlorine or ammonia) added during the water treatment process.
4.HVAC (Heating, Ventilation, and Air Conditioning) Systems
Temperature Control and Airflow Regulation: Used in air conditioning systems to regulate the flow of cooling or heating fluids to maintain the desired temperature.
Pressure and Airflow Regulation: Adjusts the flow and pressure of air in ventilation, air conditioning, and humidification systems to ensure indoor comfort.
5.Food and Beverage Industry
Liquid Flow Control: Precisely controls the flow of liquids in processes such as brewing, dairy production, and beverage bottling.
Temperature and Pressure Regulation: Regulates temperature and pressure during heating, cooling, and sterilization to ensure product quality and safety.
6.Pharmaceutical Industry
Precision Flow Control: Regulates the flow of liquids and gases in pharmaceutical manufacturing processes to ensure precise control of process parameters.
Pressure Control: Adjusts pressure in cleaning and sterilization systems to ensure stable system operation.
7.HVAC Systems
Airflow and Temperature Control: Controls the flow and temperature of air to adjust environmental conditions, ensuring comfort and energy efficiency inside buildings.
8.Steel and Metallurgical Industry
Gas Flow Control: Precisely adjusts the flow of gases such as oxygen and nitrogen during smelting and heating processes to ensure stable furnace temperatures and chemical reactions.
Cooling Fluid Flow Regulation: Regulates the flow of cooling fluids in cooling systems to ensure temperature control of equipment.
9.Thermal and Power Industry
Steam and Water Flow and Pressure Control: Regulates the flow of steam and water in boiler systems, heat exchangers, and power plants to ensure efficient operation of thermal systems.
10.Mining Industry
Slurry Flow Regulation: Adjusts the flow and pressure of slurry during transportation and separation processes to ensure efficient extraction and processing of minerals.